Our Factory
Bulletproof Helmet Production Line
1. Helmet Design: The initial step involves designing the bulletproof helmet, taking into consideration factors such as material selection, shape, size, and weight distribution. This step may involve collaboration between designers, engineers, and ballistic experts.
2. Material Preparation: The chosen materials, such as advanced ballistic fibers (e.g., Kevlar) and composite materials, are procured and prepared for production. This may involve cutting, shaping, and treating the materials to meet the required specifications.
3. Helmet Shell Formation: The helmet shell is formed by using various techniques such as molding or vacuum forming. This process involves heating the materials and shaping them into the desired helmet shape using molds or specialized machinery.
4. Helmet Assembly: In this step, different components of the helmet are assembled. This includes attaching the helmet shell to the inner padding, chin strap, visor, and other required accessories. The assembly process may involve the use of adhesives, fasteners, or specialized bonding techniques.
5. Ballistic Insertion: A key aspect of a bulletproof helmet is its ability to withstand ballistic impact. This step involves inserting ballistic inserts, typically made of multiple layers of ballistic fibers or other specialized materials, into the helmet shell. The inserts are precisely positioned and secured within the helmet to provide optimal protection.
6. Quality Control: Throughout the production process, quality control measures are implemented to ensure that each helmet meets the required standards. This may involve inspections, testing for ballistic performance, weight checks, and overall functionality assessments.
7. Finishing and Packaging: Once the helmets pass the quality control checks, they undergo finishing processes such as cleaning, polishing, and painting, if necessary. The finished helmets are then packaged appropriately to protect them during storage and transportation.
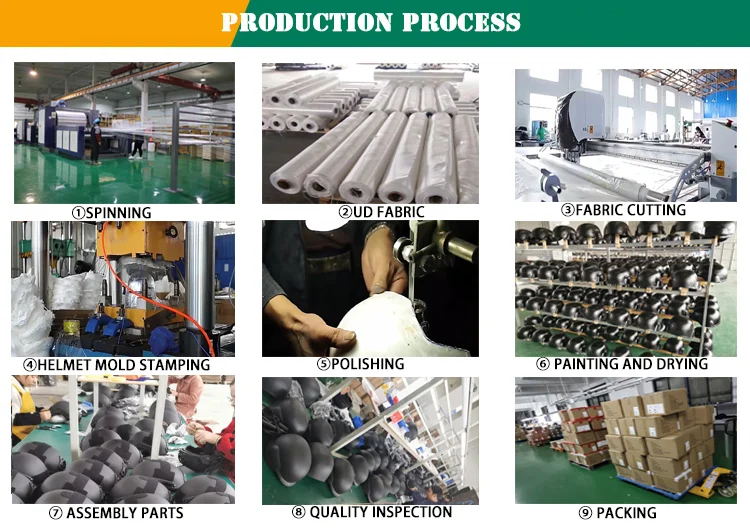

Bulletproof Plate Production Line
1. Material preparation: The first step involves gathering the necessary materials for the bulletproof plates. These materials often include ballistic fibers such as aramid or ultra-high molecular weight polyethylene (UHMWPE), as well as resin matrices and other additives.
2. Fiber cutting and alignment: The ballistic fibers are cut into specific lengths and aligned in a particular arrangement to ensure optimal strength and performance. This step may involve processes such as weaving or layering the fibers.
3. Prepreg formation: In this step, the cut and aligned fibers are impregnated with resin to create prepreg sheets. The resin helps bond the fibers together and provides additional structural integrity.
4. Lay-up and stacking: The prepreg sheets are carefully laid out and stacked together according to the desired thickness and configuration of the bulletproof plate. This process may involve alternating layers of fiber orientations to enhance the plate’s resistance to different types of ballistic threats.
5. Pressing and consolidation: The stacked prepreg layers are placed into a mold or press and subjected to heat and pressure. This process helps consolidate the layers, remove any air voids, and ensure proper bonding between the fibers and resin. The specific temperature and pressure parameters are determined based on the materials used.
6. Curing: Once the pressing process is complete, the mold or press is heated to initiate the curing process. Curing involves maintaining the plates at a specific temperature for a predetermined duration to allow the resin to fully harden and cure. This step is crucial for achieving the desired mechanical properties of the bulletproof plate.
7. Trimming and finishing: After the curing process, the bulletproof plates are carefully removed from the mold or press. Any excess material is trimmed off, and the edges are shaped and smoothed to achieve the desired final dimensions and appearance.
8. Quality control and testing: The finished bulletproof plates undergo rigorous quality control and testing procedures to ensure they meet the required standards and specifications. This may include conducting ballistic tests to evaluate their resistance to projectiles and verifying other mechanical properties.
9. Packaging and distribution: Once the bulletproof plates pass the quality control tests, they are packaged and prepared for distribution to customers. The plates are typically labeled and stored appropriately to maintain their integrity until they reach the end-users.
Bulletproof Vest Production Line
1. Material Selection: Choose the appropriate materials for the vest, such as ballistic fabrics, Kevlar, or other high-strength synthetic fibers.
2. Cutting and Shaping: Cut the selected materials into specific patterns and shapes according to the design of the vest components, including the front and back panels, collar, and side straps.
3. Stitching and Sewing: Use industrial sewing machines to join the cut pieces together, creating the various sections of the bulletproof vest. This step involves precise stitching to ensure durability and strength.
4. Panel Assembly: Assemble the front and back panels, which contain multiple layers of ballistic materials, and stitch them together securely. This step creates the primary protective layers of the vest.
5. Attachment of Additional Components: Attach additional components to the vest, such as shoulder straps, side straps, collar, and pockets for accessories. These components enhance the vest’s functionality and comfort.
6. Reinforcement and Edge Binding: Reinforce critical areas of the vest, such as the edges, seams, and attachment points, to increase durability and prevent fraying. Edge binding with sturdy fabric or binding tape helps protect the raw edges.
7. Inspection and Quality Control: Thoroughly inspect each completed vest for any defects or inconsistencies. This step ensures that the vests meet the required quality standards and are ready for the next phase.
8. Packaging and Labeling: Package the bulletproof vests with inappropriate materials to protect them during transportation and storage. Affix labels with relevant information, such as size, model, and manufacturing details, for easy identification.
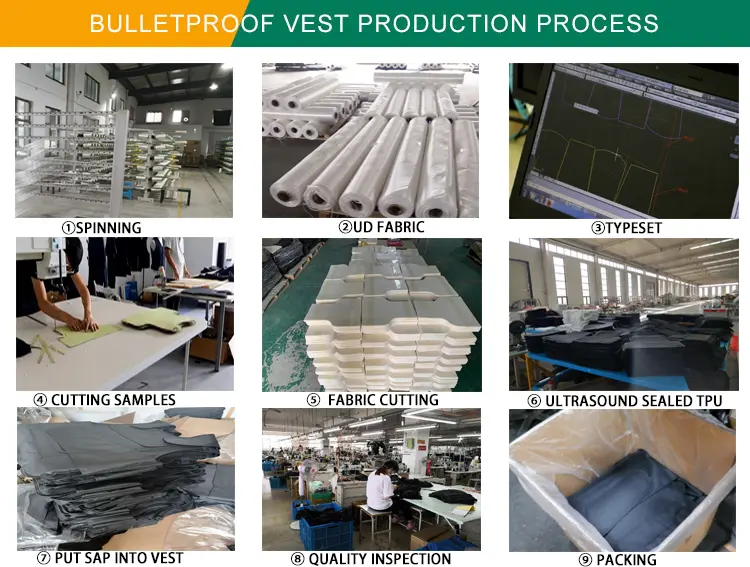
Contact Us
- 0086 21 57680930
- 0086 15800356957
- frank.ma@sturdyarmor.com
- Building 24, 66 Guangfulin East Road, Songjiang District, Shanghai, CN